Contents
Many warehouse managers use automation technology to cut expenses, increase operational effectiveness, and maintain competitiveness. Barcode scanning is still one of the most often used of these technologies. A successful warehouse must coordinate shipping, receiving, restocking, picking, and packing processes that frequently happen simultaneously. Using barcodes makes moving items between locations inside and outside a warehouse simple, providing a unique identity for every rack, container, or item. Thus, barcode technology became a crucial component of effective inventory management and has developed into a dependable and practical method of tracking products.
How to Set Up a Barcode System for the Warehouse?
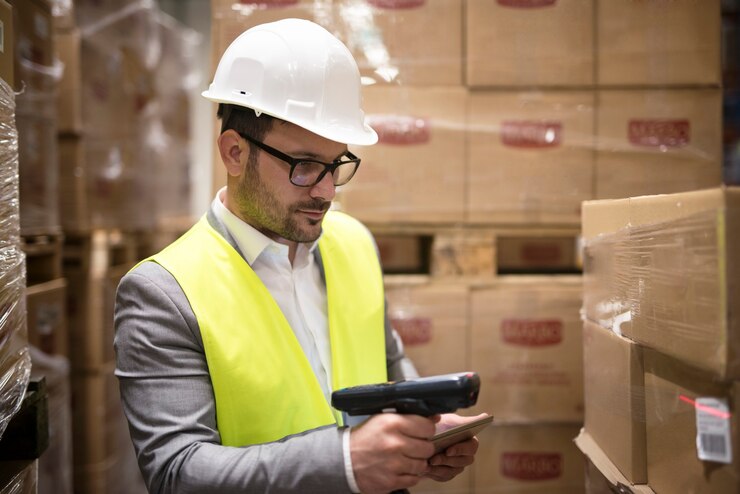
Many factors must be considered before, during, and following the implementation of barcodes. Creating a plan that covers choosing the right barcoding hardware and software for your warehouse’s unique needs and allows easy implementation are the most important ones. This guide will assist in outlining the essentials required for a smooth transition in three simple steps, whether you know something or barely anything on the topic.
1. Pick the Correct Barcode Hardware and Software
Before you start with an initial plan, you must know your options regarding the different hardware and software components to help prevent future issues and ensure compatibility.
Barcode Scanners
Understanding the different options available on the market when browsing the range of easy-to-use and reliable barcode scanners online is crucial to choosing an alternative compatible with your needs and ensuring a smooth process. However, given the various types available, it can be rather challenging.
Barcode Decoding Capability
First things first, you must select a design for your barcode labels, as the type of decoding capability is the most important factor to consider. One-dimensional (1D) and two-dimensional (2D) barcode designs are possible. A 1D barcode encodes either alpha-numeric (letters and numbers) or numeric (numbers alone) data using vertical lines of different widths. 2D barcode designs like the widely used QR code encode data using boxes
Connectivity
While a straightforward Bluetooth-enabled scanner is sufficient for most warehouses, planning for future growth by opting for versatile models is always wise. Scanners must meet some basic criteria: read barcodes accurately on the first attempt, work seamlessly at distances ranging from 3 to 60 cm, and feature a visible laser beam that activates when triggered. Anything less risks frustrating staff and slowing workflows.
Technology
You’ll also need to decide between two main scanner technologies: laser and image-based. Laser scanners excel in reading barcodes from a distance, up to 60 cm away, but their moving parts make them less durable in tough environments. On the other hand, image-based scanners, which use cameras to capture barcode images, are more robust and cost-effective but require closer proximity to barcodes.
Environment
Durability is crucial, especially in demanding environments, so choose a model that withstands rough handling or extreme temperatures.
Portability
Wireless handheld (and wearable) barcode scanners online available are often ideal, especially in large warehouses. Ensuring the scanner integrates seamlessly with your inventory management software is critical to avoid future compatibility headaches. In contrast, desktop scanners aren’t meant to be picked up frequently. They could therefore not be appropriate for uses involving large, heavy, or bulky objects that are challenging to transport to the scanner.
Software
Warehouse Management Systems (WMS), Computerised Maintenance Management Systems (CMMS) software (see more about what a CMMS is), and Enterprise Asset Management Systems (EAM) are the most widely used inventory and asset management platforms in warehouses.
You need to review your existing software platform’s requirements to find out which barcode symbologies and barcode scanners are compatible with it.
Barcode Printer
Dot matrix printers are unsuitable for barcodes due to poor quality and slow speed, while inkjet and laser printers face issues like high memory usage, slow printing, and limited material compatibility. Thermal printers stand out for their speed, quality, and ability to print on various materials.
When selecting the ideal label printer, consider direct thermal models for low-maintenance, short-term labels or thermal transfer options for durable labels in harsh environments. Additionally, evaluate factors like resolution (measured in DPI), memory capacity (RAM and flash), label width, and printing speed to match your specific needs.
2. Determine Your Needs
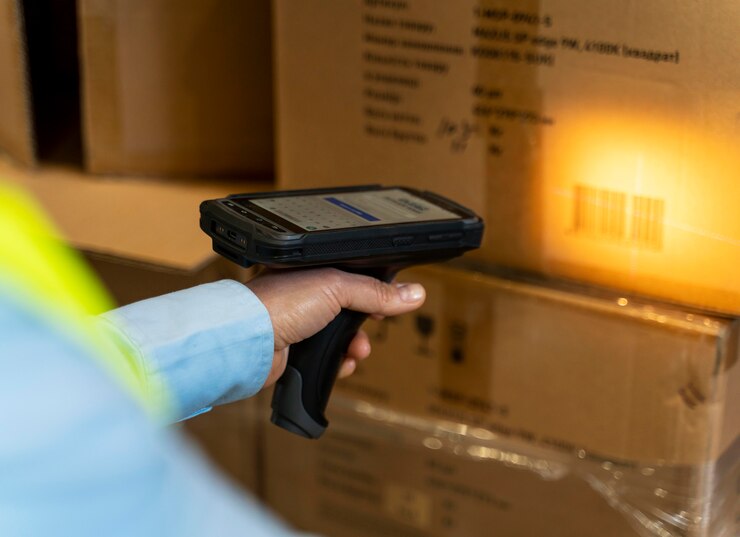
You must determine your warehouse’s needs to choose the right hardware and software pieces for barcoding and implement it successfully. To do that, create a list of all SKUs and variants in the warehouse, including planned ones. Use manufacturers’ barcodes where possible and ensure each item has a unique barcode and assigned storage location. Implement a process for inspecting and scanning items upon arrival and shipment.
Evaluate transport routes, shelving, and rack structures to decide where to place barcodes. For raised racks, either use duplicate barcodes at ground level or invest in long-range scanners. Identify key locations like aisles, cold storage, and docks for clear labelling.
If handling bulk containers like IBCs or pallets, ensure barcodes distinguish them from individual items. Review barcode symbologies to align scanning systems with supply chain partners.
3. Opt for Easy Implementation
To implement a barcode system, establish processes for applying labels, updating software, and scanning items. Place barcodes thoughtfully to ensure they are unobstructed and easy to scan.
Integrating barcodes with a central WMS provides real-time data access, enabling employees and managers to monitor KPIs like safety stock and inventory turnover. This data helps set priorities, measure results, and improve training for the team.
Schedule regular reviews of warehouse data to identify and address issues during the transition period, ensuring smoother workflows and efficient operations.