Every job has its risks, but some require more protection than others. Take welding as an example – given that it’s to do with joining metals together, like aluminium parts, it’s a process that relies on a lot of use of heat and pressure. Since there are arcs that result from this joining, doing everything you can to protect the eyes is considered a necessary safety measure.
What happens if you don’t wear glasses when welding? Let’s just say eye injuries are guaranteed. As to what kind and how severe, it depends on the level of exposure. The radiant energy that’s the result of the welding causes a condition known as welders’ eye or welders’ flash, which is the injury to the surface, the conjunctiva.
Not to mention, there’s flying metal debris you need to beware too. Besides pain, swelling, and blurry vision, temporary blindness, more serious UV radiation (as bright as the sun) and exposure to metal dust can also lead to permanent blindness. Why go through this risk, when you can get the protection you need from a hard-coated and anti-fog welding lens created to shield your eyes?
Shade
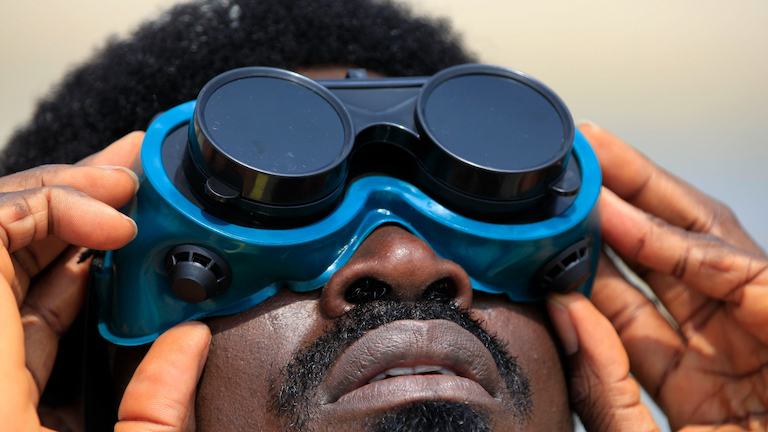
The reason there are many types of lens shades available has to do with the different welding tasks they’re designed for. Some jobs don’t require as much protection as others, so you should consider your line of work and the potential hazards to choose a suitable shade. On a scale from 3 and 4 to 13 and 14, the higher the number, the bigger the protection.
As such, the lowest 3 and 4 are ideal for welding tasks with minimal radiation where there’s no risk of sparks, whereas the highest 13 and 14 are meant for the heavy-duty welding tasks with intense radiation. Each of these is designed so as to protect the eyes and provide optimal visibility, enabling you to carry on with your job with utmost efficiency.
If you want to get the best of both worlds, you should consider the auto-welding lens that darkens itself when needed. Speaking of shade, there’s another distinction you should be aware of. Besides the clear lens, you can come across green, cobalt blue, super blue drop-in, gold, super magenta drop-in, and alloweld lens models.
Out of these, the green is great for different work environments and glare reduction, whereas both the cobalt blue and super blue are ideal for precision tasks and contrast, as well as for reducing eye strain and fatigue. The gold is fit for specialised applications when welding, the super magenta for colour differentiation, and the alloweld for intense light and radiation.
For those tasks that require extra detail work and precision, you should consider getting a specialised magnifying lens. This is the type that comes equipped with built-in magnification diopters to provide you with the needed vision boost for the most delicate of details like creating fine weld seams.
Protection Level
It all comes down to how risky your line of work is on a daily basis. You have to evaluate your exposure to intense light, focusing on the UV radiation, as well as whether or not you work around flying metal debris to decide on the protection level your lens should offer you. Mind you though, this doesn’t only refer to the shade, but also to the size and coverage.
As such, you can find welding lenses in varying sizes, fit for welding glasses, welding goggles, and even welding helmets and welding face shields. To be able to narrow down the options, it’s important to evaluate not only the risks and safety requirements but also your peripheral vision and the level of comfort a certain type of lens size offers you. If you wear prescription glasses, this is another aspect you should consider when choosing your ideal welding lens protection.
Compliance With Safety Standards
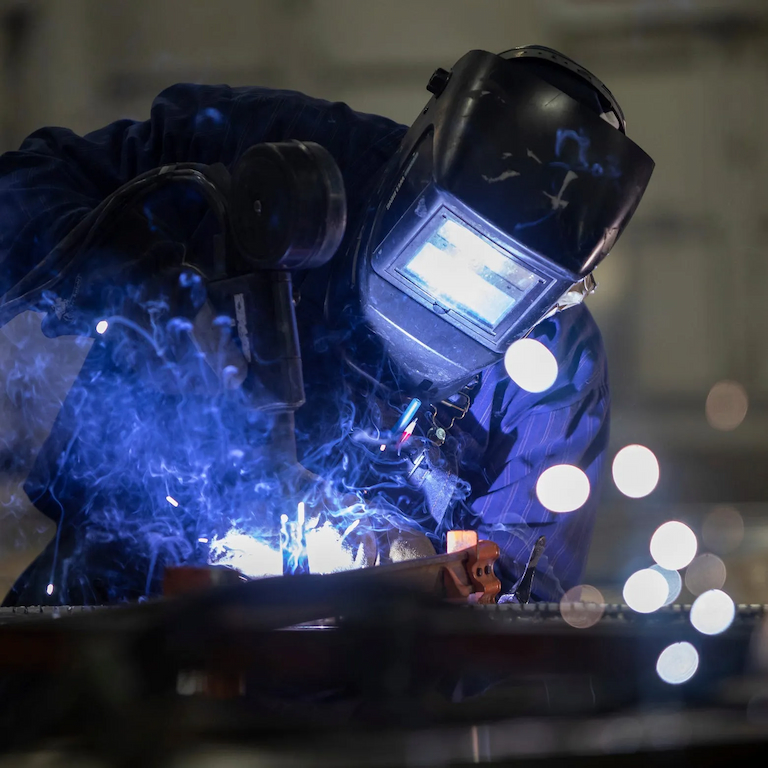
Moreover, as you do the choosing from a range of welding lens products, it’s advisable to pay attention to the manufacturing, and whether or not the chosen product aligns with the Australian safety standards, particularly AS/NZS 1337. This would give you an additional level of peace of mind. For extra precaution, it’s also advisable to check the WHS (Work Health and Safety) recommendations so you meet and exceed the minimum safety requirements.
Material
The market is abundant when it comes to material options too, specifically the lenses made of polycarbonate and glass. Out of these two, the polycarbonate offers advantages like impact-resistance and lightweight properties, fit for the particularly rugged environments, whereas glass is better in terms of scratch-resistance and optical clarity.
Of course, both materials have their own set of drawbacks too. For instance, polycarbonate lenses are not as scratch-resistant as glass and may require frequent replacements due to wear and tear. On the other hand, glass lenses can shatter upon impact, posing a potential danger for the wearer but can also be heavier, causing discomfort for some individuals.