A press brake offers precision and control in bending metal sheets into the desired shapes. It shapes metal into precise angles and forms by clamping the workpiece between a top tool and a matching bottom die. This makes it a crucial tool for industries ranging from automotive to construction. However, using it effectively requires more than just operating the machine – it involves understanding proper setup, tooling selection, and safety measures to achieve accurate and consistent results.
When it comes to metal fabrication, a versatile press brake machine is a solid choice for any project. Whether you’re working with stainless steel, aluminium, or other metals, these machines can handle a variety of materials with precision and ease. These fabrication tools cater to different bending requirements. From simple bends to complex components, they offer the control and accuracy you need to shape metal exactly how you want it. With hydraulic NC and CNC options available, you get advanced features that allow for smooth operation and high efficiency, no matter the complexity of the task.
How to Choose the Right Tooling
When it comes to selecting the right tooling for a press brake, there’s a lot more to consider than just picking something off the shelf. The material and hardness of the tooling play a huge role in how well it performs and how long it lasts. If you’re working on heavy-duty applications, hardened steel is a solid choice because of its durability and resistance to wear.
On the other hand, carbide tools are known for their extreme hardness and ability to withstand repeated use with precision, making them perfect for high-accuracy bending tasks. For instance, if you’re working with thick stainless-steel sheets, using hardened steel tools can help prevent premature wear and keep your workflow smooth.
Tool hardness is another key factor that ensures your press brake machine performs at its best. The tougher the tool, the better it resists wear, but there’s a trade-off – higher hardness can also mean increased brittleness. A good balance is essential. A Rockwell hardness of around 60 HRC is generally ideal for handling high-strength materials without the risk of cracking under pressure.
Beyond material and hardness, coatings can make a huge difference. Options like titanium nitride (TiN) or diamond-like carbon (DLC) reduce friction and extend the life of the tooling. In a high-volume production setting, a TiN-coated tool can last up to three times longer than an uncoated one, which translates to fewer replacements and lower costs over time.
Of course, tooling has to match the material you’re working with. Softer metals like aluminium bend easily, while tougher materials like stainless steel require stronger, more resilient tooling. A thin aluminium sheet might not put much strain on the tool, but a thick steel plate needs something more robust to handle the extra force without deforming or failing. A 10mm steel plate, for example, requires far more tonnage and a stronger tool compared to a delicate 2mm aluminium sheet.
Types of Bending Dies
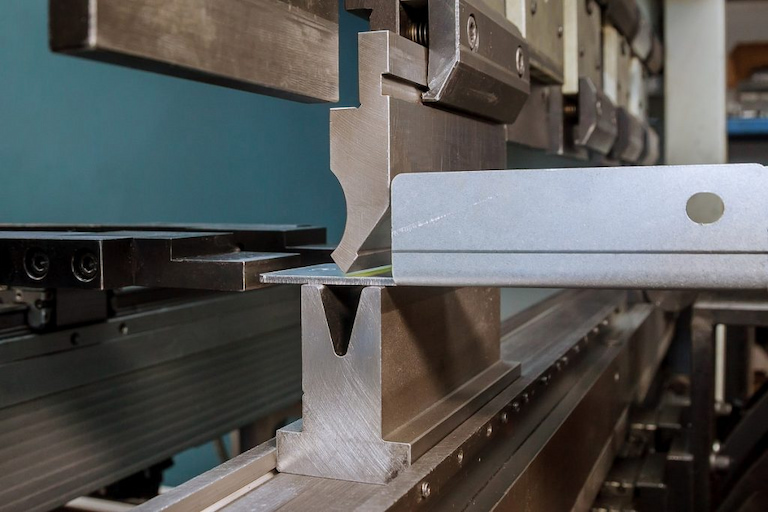
The punch and die combination determines the precision and efficiency of press brake machines. Here are some commonly used bending dies and what they bring to the table:
-Punches and dies: These are the backbone of any setup. The punch is the upper tool that applies force, while the die sits below, shaping the bend. Choosing the right pair ensures clean, accurate results;
-V-Dies: A go-to option for air bending, V-dies come in different sizes to accommodate various material thicknesses and bend angles. They’re versatile and widely used across different fabrication projects;
-Gooseneck punches: If you’re working with deep bends and need to avoid interference from the punch body, gooseneck punches are a great solution. Their curved design allows for more flexibility when forming intricate shapes;
-Acute angle punches and dies: When you need sharper bends or angles less than 90 degrees, these specialised tools get the job done. They’re perfect for applications requiring tight, crisp angles.
How Do You Use a Press Brake?
Getting the best results from a hydraulic press brake starts with proper setup and careful operation. Whether you’re working on automotive parts, industrial components, or custom pieces, it’s essential to ensure correct tooling, material alignment, and machine calibration. Following the right steps ensures precision, safety, and efficiency:
-Check the machine first: Before anything else, inspect the machine for wear, damage, or leaks. Make sure all safety guards are in place and that the emergency stop buttons are working. A quick once-over can prevent costly mistakes later;
-Set up your tooling correctly: The punch and die are the heart of the operation, so they need to be in top shape. Ensure they’re properly aligned, securely fastened, and matched to the material and bend angle you’re working with. Even a slight misalignment can throw off your results;
-Prepare your workspace: A clean, organised area makes everything run smoothly. Keep walkways clear of clutter, avoid over-lubrication on moving parts, and make sure your materials are easy to access;
-Dial in the machine settings: Adjust the back gauge for precise positioning and set the ram stroke depth according to your material thickness. For CNC press brakes, input the correct parameters to let the machine do the work for you;
-Start bending: Place your metal sheet securely on the bed, align it with the back gauge, and initiate the bend using the controls. Keep an eye on the process and listen for anything unusual;
-Inspect your work: Once the bend is complete, check the accuracy of the angles and dimensions. If adjustments are needed, tweak the settings before moving on.